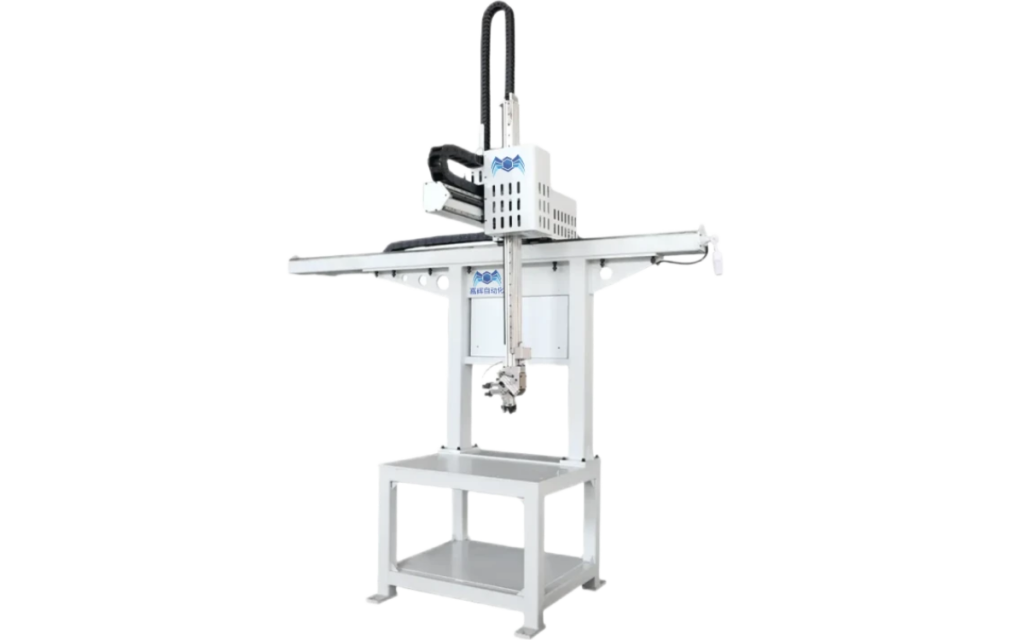
在高端精密零件加工领域,微米级的精度误差可能意味着数千件产品的批量报废。而传统数控车床依赖人工上下料的模式,不仅难以保障一致性,更成为制约高端制造产能的“隐形枷锁”。数控车床桁架机械手通过全闭环控制与智能传感技术的深度融合,正在重塑精密制造的边界——从“人机协作”到“完全自主”,推动机床上下料环节迈向真正的“零干预”时代。
一、精度革命:微米级误差的终结者
精密轴类、航空紧固件等高端工件的加工,对上下料定位精度要求苛刻(通常≤±0.02mm)。人工操作易受疲劳、视线遮挡等因素干扰,而桁架机械手凭借三大核心技术突破,彻底消除人为误差:
- 全闭环反馈系统:内置高分辨率光栅尺,实时校正伺服电机位移偏差,定位精度可达±0.01mm,媲美五轴加工中心性能;
- 动态补偿算法:针对长臂展桁架可能产生的挠度变形,通过力学模型预判并补偿轨迹偏移,确保末端执行器在3米行程内精度损失<5μm;
- 视觉纠偏模块:选配工业相机对工件姿态进行二次校验,自动调整夹取角度,解决毛坯来料位置偏差导致的撞机风险。
二、效能跃迁:从“单点突破”到“系统最优”
许多企业误将自动化改造等同于“机械手换人”,却忽视设备与生产系统的全局协同。桁架机械手的真正价值在于:
- 无缝对接数控系统:通过EtherCAT总线直接读取机床G代码,预判加工剩余时间并提前规划上下料路径,减少空行程等待;
- 能源利用率优化:采用再生制动技术回收机械臂减速时的动能,配合低功耗待机模式,较传统关节机器人节能30%以上;
- 数据驱动决策:内置振动传感器监测导轨磨损状态,结合加工节拍历史数据,主动提示预防性维护窗口,降低突发故障率。
三、场景攻坚:特殊工艺的定制化突围
面对高温锻件、超长棒料等特殊工况,标准桁架机械手往往“水土不服”。行业领先企业已推出场景化增强方案:
- 耐高温改造:抓取端配备陶瓷隔热层与循环水冷系统,可耐受800℃高温锻件的连续抓取,寿命较普通机型延长5倍;
- 长料自适应:针对3米以上棒料加工,开发双机械手协同送料系统,通过激光测距实时调整支撑间距,避免材料弯曲变形;
- 微量润滑兼容:在切削油雾环境中采用气密封结构,核心部件镀镍防腐蚀,确保10万小时免维护运行。
四、成本重构:中小企业的“轻量化”升级路径
过去,桁架机械手被视为大型企业的专属配置。如今,模块化设计与柔性付费模式正打破这一认知:
- 按需扩展架构:基础版仅包含单轴机械臂与基础夹具,后续可叠加视觉系统、多机联动模块,初期投资降低至15万元以内;
- 免编程操作:通过示教器录制人工操作轨迹,自动生成优化路径代码,无需专业工程师即可完成部署;
- 共享产能服务:针对季节性订单波动,支持短期租赁机械手并接入云端调度平台,实现“淡季零闲置,旺季弹性扩产”。
【结语】
数控车床桁架机械手的技术进化,本质是让自动化回归“解决问题”的本质——不是用复杂技术堆砌噱头,而是以极简设计直击效率、精度与成本的痛点。在制造业存量竞争时代,这套系统既是精密加工企业守住利润红线的“护城河”,更是中小厂商打破规模壁垒的“公平砝码”。当“零干预”成为车间常态,中国智造的下一程,必将由这些沉默的钢铁臂膀悄然推动。
该内容为原创,转载请注明:http://www.zdh360.com/ 嘉辉上下料车床桁架机械手