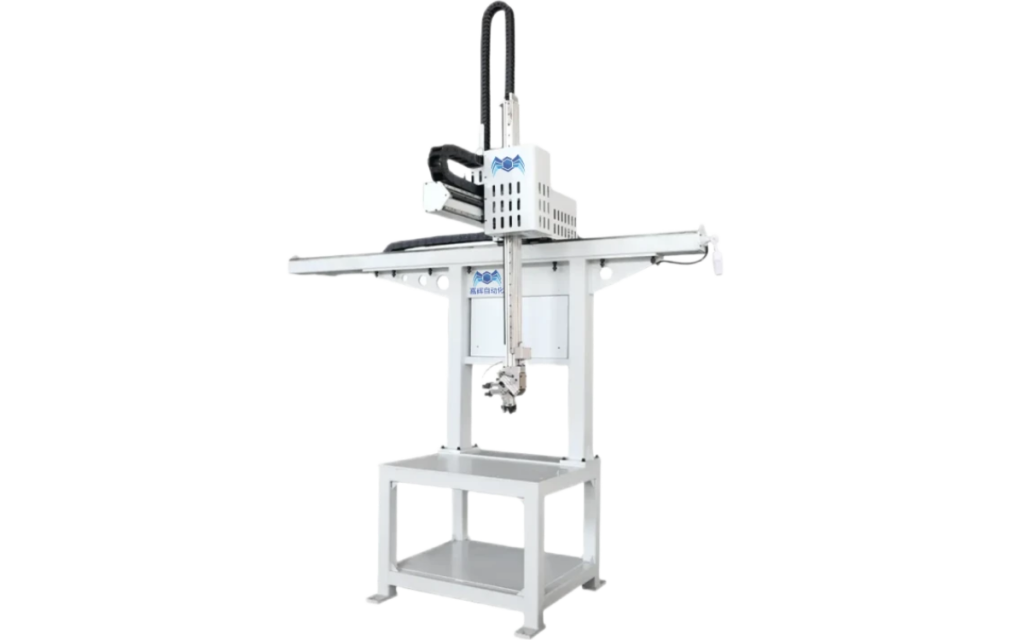
在制造业向智能化升级的浪潮中,数控车床的高效运转与人工上下料的效率瓶颈矛盾日益凸显。传统人工操作不仅依赖熟练工经验,更面临劳动强度大、换产周期长、安全隐患多等痛点。数控车床桁架机械手凭借其高精度、强稳定性和柔性适配能力,正成为推动机床行业自动化转型的核心装备,助力企业实现“无人化车间”的关键跨越。
一、结构革新:桁架机械手的“刚柔并济”设计
数控车床桁架机械手以模块化桁架结构为核心,通过横梁、立柱与导轨的刚性组合,构建覆盖机床加工区域的三维运动空间。其核心优势在于:
- 高刚性轻量化:采用航空铝材或碳钢焊接框架,在保障负载能力(可达500kg)的同时降低惯性损耗,重复定位精度稳定在±0.05mm以内;
- 多轴协同控制:X/Y/Z三轴伺服驱动系统与数控车床PLC无缝交互,支持复杂轨迹规划和速度自适应调节,满足不同规格工件的抓取需求;
- 柔性夹具系统:针对轴类、盘类等异形工件,可快速更换气动夹爪、电磁吸盘或定制化夹具,适配多品种小批量生产场景。
二、效率跃升:从“单机孤岛”到全链路自动化
传统数控车床依赖人工上下料,单台设备需频繁停机等待,实际有效加工时间不足60%。而桁架机械手的介入,可打通“毛坯上料-机床加工-成品转运”的全流程自动化闭环:
- 精准时序同步:通过光电传感器与机床信号实时交互,在主轴停转瞬间完成开舱门、取件、送料动作,单次循环节拍缩短至8秒以内;
- 多机协同作业:单套桁架系统可串联2-4台数控车床,通过智能调度算法优化任务分配,设备利用率提升至85%以上;
- 24小时连续生产:适应夜班无人值守模式,减少因人员疲劳导致的停机事故,年产能同比提升超200%。
三、场景赋能:破解复杂工况下的落地难题
数控车床桁架机械手的价值不仅在于效率提升,更在于其对严苛工业场景的深度适配:
- 油污环境耐受:关键部件采用IP65防护等级,导轨配备自清洁刮屑装置,确保切削液、金属碎屑环境下长期稳定运行;
- 安全冗余设计:集成急停按钮、防撞传感器与双回路气路保护,在意外断电或气压不足时自动锁止机械臂,避免工件坠落风险;
- 快速换型支持:通过预设程序库一键切换加工参数,配合视觉定位纠偏功能,实现不同批次工件的“分钟级”换产。
四、案例实证:某精密部件企业的降本增效之路
浙江某汽车零部件制造商引入桁架机械手后,其数控车床产线呈现颠覆性变革:
- 人力成本削减:4台机床的上下料岗位从8人减少至1人(仅负责巡检),年节约人工成本超60万元;
- 良品率提升:机械手精准定位避免人工放置偏差,关键尺寸合格率从92%提升至99.5%;
- 投资回报显著:项目整体回本周期缩短至14个月,产能扩充后新增年订单额突破800万元。
【结语】
数控车床桁架机械手并非简单的“机械替代人工”,而是通过高可靠性硬件与智能化控制系统的深度融合,重构机床加工的价值链。在工业4.0与“中国制造2025”战略驱动下,这一技术已成为企业突破产能天花板、应对劳动力短缺的必选项。未来,随着模块化设计与边缘计算技术的进一步渗透,桁架机械手将向更轻量、更敏捷的方向进化,持续释放数控机床的潜能。
该内容为原创,转载请注明:http://www.zdh360.com/ 嘉辉上下料车床桁架机械手