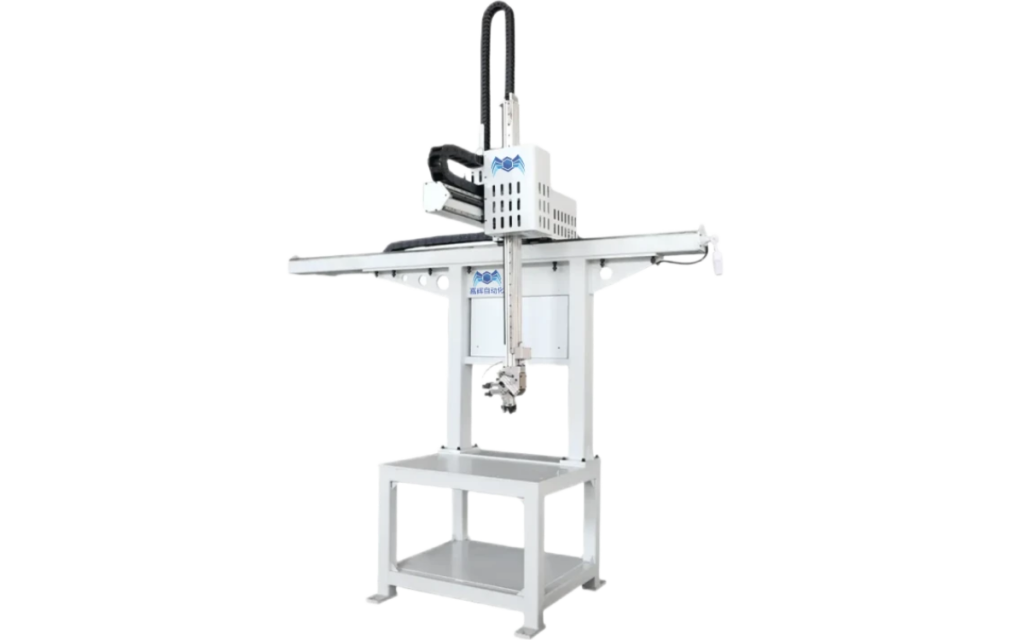
导语
在工业4.0背景下,数控机床作为智能制造的核心载体,其上下料环节的效率直接决定了整条产线的综合竞争力。数控机床桁架机械手通过融合AI视觉、数字孪生等先进技术,已从单纯的“机械臂”进化为具备自主决策能力的“智能节点”。本文将聚焦其智能化创新路径与跨行业落地实践,揭示其对制造业转型升级的战略意义。
一、智能化升级:桁架机械手的“大脑革命”
1. 感知层:从“盲操作”到“毫米级视觉定位”
- 多模态传感系统:集成激光雷达+工业相机,支持工件三维建模与姿态识别,定位精度达±0.005mm;
- 深度学习算法:通过历史加工数据训练模型,可自动识别工件缺陷并触发异常处理机制;
- 实时反馈网络:基于5G专网传输,将采集数据同步至云端控制平台,延迟低于20ms。
2. 决策层:AI赋能的动态优化能力
- 路径规划引擎:采用RRT*算法生成最优运动轨迹,避开机床刀具区域,效率提升30%;
- 自适应加工参数调整:根据材料硬度、刀具磨损状态动态优化切削速度与进给量;
- 预防性维护预警:通过振动频谱分析预测轴承寿命,提前45天发出备件更换建议。
二、跨行业应用:从“汽车零件”到“芯片晶圆”的全覆盖
1. 汽车制造:薄壁件加工的“防变形专家”
- 应用场景:发动机缸盖去毛刺、铝合金轮毂抛光
- 技术亮点:
- 气浮导轨+负压吸附装置,确保薄壁工件(厚度≤1mm)加工不变形;
- 动态力补偿技术,将加工振动抑制在±5μm以内。
2. 3C电子:精密微小零件的“纳米级操控”
- 应用场景:手机摄像头模组装配、PCB板激光打孔
- 技术亮点:
- 微型伺服电机(扭矩分辨率≤0.1N·mm)实现±0.02mm重复定位;
- 防静电手腕设计,满足ISO 14644 Class 5洁净室标准。
3. 航空航天:特种材料加工的“高温耐受者”
- 应用场景:钛合金叶片榫槽加工、碳纤维复合材料钻孔
- 技术亮点:
- 主轴同步冷却系统,通过红外热成像实时监控刀具温度;
- 多段式真空吸附夹具,适应异形曲面工件的非刚性抓取。
三、数据驱动:桁架机械手如何创造真实效益
1. 成本对比分析(某家电企业案例)
项目 | 改造前(人工操作) | 改造后(桁架机械手) |
---|---|---|
单件耗时 | 45秒 | 18秒 |
年人力成本 | 28万元 | 8万元 |
不良品率 | 3.2% | 0.5% |
设备利用率 | 65% | 92% |
2. ROI测算模型
- 投资回收期:约14个月(按年产20万件计算);
- 增值收益:通过工艺优化使产品合格率提升2.7%,年增收超500万元。
四、技术避坑指南:企业选型的三大关键
1. 核心误区警示
- 过度追求速度:忽视刚性设计导致加工精度下降(某企业曾因选型不当报废300万元设备);
- 忽视软件生态:封闭式控制系统难以对接MES系统,造成数据孤岛;
- 忽略安全冗余:未配置双重安全回路,曾引发重大安全事故。
2. 成功选型四步法
- 需求拆解:明确加工工件的尺寸范围(长宽高×重量)、材质特性、工艺要求;
- 现场验证:要求供应商提供72小时实机测试报告(包含振动频谱、温升曲线等);
- 接口兼容性检查:确认是否支持EtherCAT总线、Profinet等主流工业协议;
- 售后服务条款:优先选择提供“5年质保+备件库本地化”的供应商。
五、前沿展望:2030年桁架机械手的三大进化方向
- 仿生柔性关节:借鉴章鱼触手研发自适应末端执行器,实现任意形状工件抓取;
- 数字孪生融合:通过虚拟调试减少现场调试时间,改造周期缩短60%;
- 绿色节能技术:采用永磁同步电机与再生制动技术,能耗降低至传统伺服系统的40%。
结语
数控机床桁架机械手正从“自动化工具”向“智能制造中枢”演进,其价值已超越单纯的成本削减,成为驱动工艺创新、提升产品竞争力的核心要素。对于正在推进数字化转型的企业而言,选择具备智能化基因的桁架机械手,不仅是技术升级的选择,更是面向未来市场竞争的战略投资。
该内容为原创,转载请注明:http://www.zdh360.com/ 嘉辉上下料机床桁架机械手