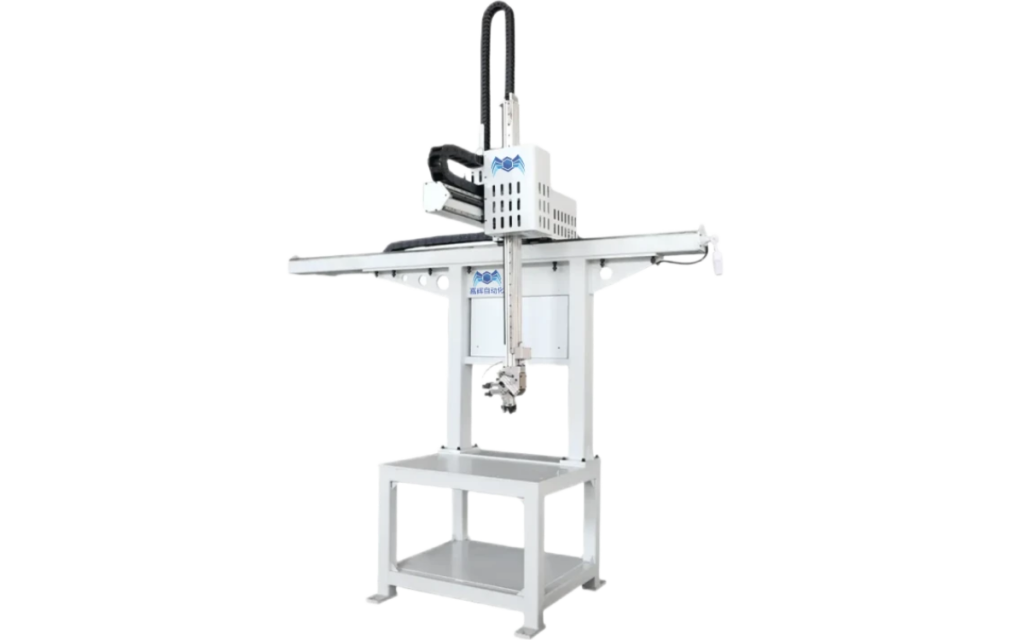
导语
在数控机床高速、高精度的加工需求下,传统人工上下料模式已难以满足现代制造业对效率、安全与稳定性的严苛要求。数控机床桁架机械手凭借其模块化设计、高精度运动控制与智能化协同能力,正成为打通“最后一米”自动化瓶颈的核心技术。本文将从技术原理、核心优势及落地价值展开深度解析……
**一、技术解析:数控机床桁架机械手如何实现“精准交付”?**
1. 结构设计:刚性框架+多轴联动
- 主体架构:采用高强度合金钢焊接成型,抗扭刚度达500N·mm²,确保长周期稳定运行;
- 驱动系统:配备绝对值编码器+谐波减速器的三轴伺服模组,定位精度±0.01mm,重复定位精度±0.005mm;
- 末端执行器:兼容真空吸盘、电磁夹爪、柔性爪头等多种工具,适配圆柱形、不规则异形工件。
2. 核心技术指标对比(与传统机械手)
参数 | 桁架机械手 | 传统关节式机械手 |
---|---|---|
节拍时间 | ≤30秒/件(高速机型) | ≥60秒/件 |
工作空间 | 可定制10-30米线性跨度 | 受限于关节旋转半径 |
抗干扰能力 | IP67防护等级,抗振动设计 | 易受车间粉尘、电磁干扰 |
二、行业痛点与桁架机械手的针对性突破
1. 精密加工场景的四大挑战
- 热变形控制:主轴高速旋转导致工件温升,人工装夹易产生应力变形;
- 多品种小批量:频繁换型导致设备空闲率高,人工操作容错率低;
- 高危操作风险:刀具飞溅、高速旋转部件易引发安全事故;
- 数据追溯需求:传统人工记录难以满足ISO 13485医疗器械质量管理规范。
2. 桁架机械手的创新解决方案
- 热补偿技术:集成温度传感器与实时补偿算法,加工误差降低至±0.003mm;
- 快速换模系统:通过气动夹具切换工具,换型时间缩短至5分钟内;
- 安全防护体系:配备多级安全联锁(光电传感器+急停按钮),符合ISO 10218安全标准;
- 数据接口开放:支持OPC UA协议与MES系统直连,实现生产全流程数字化管控。
三、实战案例:某航空航天企业应用成效
背景:
某飞机零部件厂商需加工钛合金叶片,原有工艺采用人工上下料,单件耗时2分钟,合格率仅85%。
改造方案:
部署 数控机床桁架机械手+视觉定位系统,实现:
- 自动抓取→定位→装夹全流程无人干预;
- 每分钟完成1.5次循环,产能提升400%;
- 加工一致性提升至IT7级,废品率降至1.2%;
- 通过MES系统追溯每片叶片的加工参数,满足AS9100航空质量管理体系要求。
客户反馈:“桁架机械手不仅解决了招工难题,更让我们在特种材料加工领域获得了国际客户的订单!”
**四、选型指南:如何匹配企业需求?**
1. 关键参数选择
需求类型 | 推荐机型 | 核心配置 |
---|---|---|
小型精密零件 | 轻量化桁架机械手(负载≤5kg) | 视觉引导+纳米涂层导轨 |
大型重型工件 | 重型桁架机械手(负载≥50kg) | 液压阻尼减震+齿形带传动 |
多机协同生产线 | 模块化桁架集群系统 | 5G通信+分布式控制架构 |
2. 成功要素
- 技术验证:要求供应商提供第三方检测报告(如MTBF≥8000小时);
- 售后服务:优先选择提供远程诊断+本地化服务团队的厂商;
- 成本控制:分阶段实施(先改造1-2台机床验证效果)。
五、未来趋势:桁架机械手与工业AI的深度融合
- 数字孪生技术:通过虚拟仿真优化机械手运动轨迹,减少试错成本;
- 自学习算法:基于历史加工数据预测刀具磨损,自动调整加工参数;
- 轻量化复合材料:碳纤维框架的应用将使设备重量降低30%,能耗下降15%。
结语
在智能制造升级的浪潮下,数控机床桁架机械手已不仅是自动化工具,更是企业构建柔性化、智能化产线的战略支点。通过精准解决精密加工痛点的创新技术,它正在为航空航天、医疗器械、汽车零部件等高端制造领域创造不可替代的价值。
该内容为原创,转载请注明:http://www.zdh360.com/ 嘉辉上下料机床桁架机械手