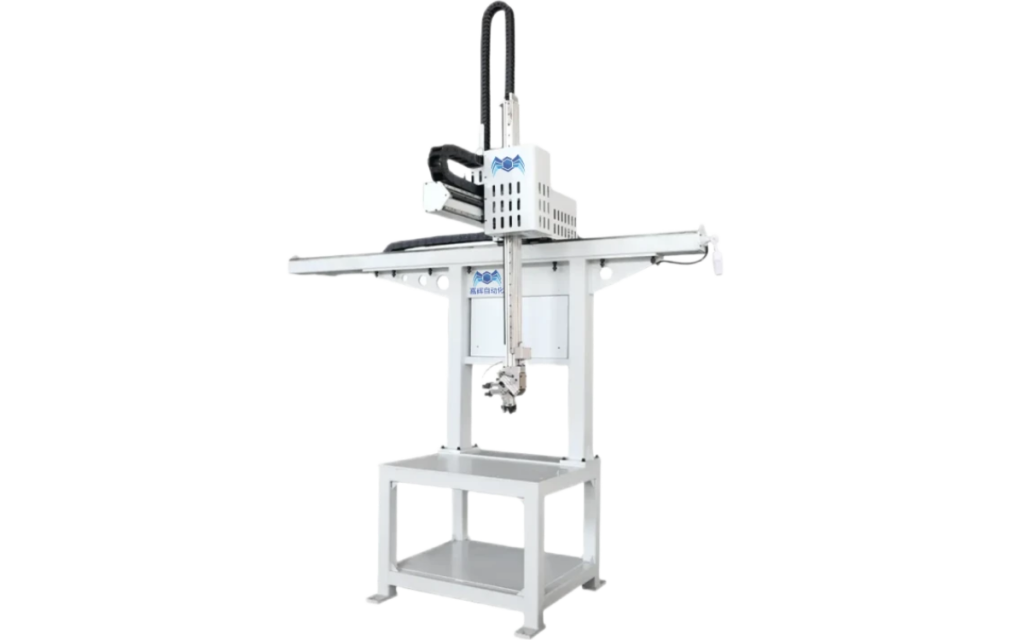
在数控机床高精度加工场景中,工件的重复定位精度、产线节拍稳定性直接决定了产品的良率与交付效率。传统人工上下料因操作波动性大、易受外部干扰等问题,难以满足精密零部件制造的严苛要求。数控机床桁架机械手凭借全闭环控制、超低振动传输、多机无缝协同等核心技术,正在成为精密加工领域实现“零误差”生产的核心装备,推动无人化产线从概念走向规模化落地。
一、精密加工之殇:人工上下料的隐形损耗
在航空航天齿轮、医疗器械金属关节等高端制造领域,工件加工精度普遍要求≤±0.01mm,但人工干预导致的隐性损耗常被忽视:
- 微米级偏差:人工放置工件时呼吸、手部抖动可能引入0.05mm以上的随机误差;
- 热传导干扰:人手接触精密毛坯造成局部温度变化,导致加工后尺寸波动;
- 节拍不可控:工人疲劳或换班导致生产效率波动20%以上。
数控机床桁架机械手通过全自动物料流转,彻底消除人为因素干扰,将加工一致性提升至99.9%,同时实现24小时不间断生产,设备综合效率(OEE)突破90%。
二、技术突围:桁架机械手的精密基因
1. 全闭环反馈系统,精度直达±0.005mm
采用光栅尺实时反馈与伺服电机动态补偿技术,机械手运动轴定位精度达±0.005mm,相当于头发丝直径的1/15。在光学镜片模具加工中,机械手可精准抓取直径30mm的钨钢毛坯并定位至机床卡盘,重复定位误差不超过2微米,确保镜面抛光无瑕疵。
2. 抑振设计与轻量化抓取,保障加工稳定性
通过桁架结构模态分析与阻尼减震优化,机械手运行振动幅度降低至0.02G以下,避免对机床切削过程造成干扰。搭配碳纤维材质夹具,抓取10kg工件时自重仅1.2kg,从源头上减少惯性冲击。
3. 多机床协同调度,产能线性倍增
一台桁架机械手可同时对接4-6台数控机床,通过中央控制系统智能分配上下料任务。例如,某阀门加工企业部署机械手集群后,6台机床的工件流转时间从8分钟压缩至45秒,日均产能提升300%,且完全杜绝了工序等待浪费。
三、场景落地:从精密部件到重型工件的全覆盖
案例1:高精密轴承套圈加工
- 痛点:人工上下料导致套圈圆度误差超0.03mm,磨削工序废品率高达8%;
- 方案:定制双Z轴桁架机械手,集成气动测头实现装夹前自动找正;
- 成效:加工圆度误差≤0.008mm,良率提升至99.6%,年节省材料成本200万元。
案例2:风电主轴超重型加工
- 痛点:单件重量1.2吨的主轴人工吊装耗时30分钟,安全隐患突出;
- 方案:开发20米跨距重型桁架机械手,配备液压缓冲夹具与双安全制动系统;
- 成效:单次上下料时间缩短至7分钟,人员工伤风险归零,加工效率提升25%。
四、持续进化:可靠性+易用性双重升级
面对制造业对设备耐久性与操作便捷性的需求,桁架机械手持续迭代:
- 关键部件寿命翻倍:采用陶瓷涂层导轨与预紧式滚珠丝杠,磨损率降低80%;
- 极简人机交互:图形化示教器支持拖拽式编程,普通工人30分钟即可掌握操作;
- 环境强适应:IP65防护等级与宽温型设计,可在-20℃至55℃车间稳定运行。
该内容为原创,转载请注明:http://www.zdh360.com/ 嘉辉上下料机床桁架机械手