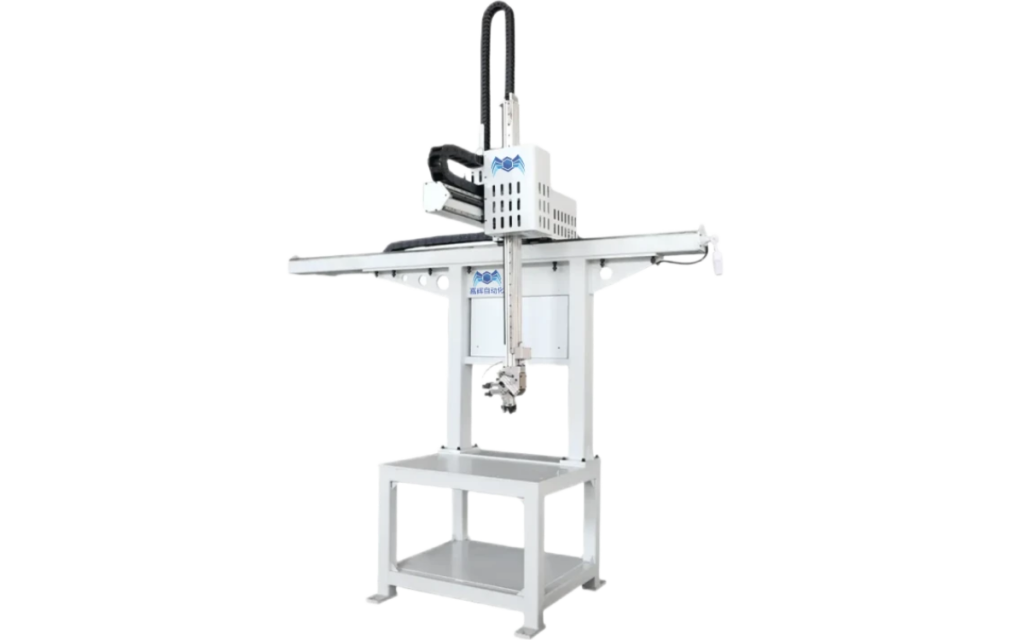
在数控机床加工领域,高效、稳定的物料搬运是保障产线连续运转的核心环节。随着制造业对精度和效率的要求日益严苛,传统人工上下料模式逐渐暴露出节奏慢、一致性差、人力成本攀升等问题。数控机床桁架机械手凭借其刚性结构、精准定位、全自动协同等特性,正成为破解行业痛点的关键技术装备,助力企业实现从“人控”到“智控”的跨越式升级。
一、直击行业痛点:人工上下料的局限性
数控机床加工往往涉及多道工序的连续作业,人工搬运不仅效率低下,还面临诸多挑战:
- 节奏不匹配:工人操作速度难以与机床加工节拍同步,导致设备空转或物料堆积;
- 精度偏差:人工放置工件易产生位置偏移,引发加工误差甚至刀具损坏;
- 安全隐患:重型工件搬运易造成工伤事故,高温、油污环境进一步加剧作业风险。
而数控机床桁架机械手通过全流程自动化替代人工干预,将上下料时间压缩至秒级,同时保障毫米级重复定位精度,真正实现“人机分离、高效协同”。
二、桁架机械手的核心技术突破
1. 高刚性结构设计,保障长效稳定运行
桁架机械手采用优质钢材或铝合金框架,通过力学仿真优化负载分布,横梁跨度可达10米以上,垂直负载能力突破500kg。其封闭式导轨与齿轮齿条传动系统,有效抵御车间粉尘、油雾侵蚀,平均无故障运行时间(MTBF)超过20,000小时,显著降低维护成本。
2. 多轴协同控制,适配复杂工艺场景
基于多轴联动伺服控制系统,桁架机械手可实现X/Y/Z三轴直线运动与旋转轴的自由组合。例如,在加工曲轴、涡轮叶片等异形件时,机械手可精准执行“抓取-翻转-二次定位”动作,配合机床自动门启闭,全程无需中断加工流程。
3. 智能感知与容错机制,提升系统可靠性
集成光电传感器与压力反馈装置后,机械手可实时监测工件抓取状态。当检测到物料缺失或位置异常时,系统自动触发报警并暂停动作,同时通过HMI界面提示故障点,缩短75%以上的排查修复时间。
三、落地应用:从单机到产线的全面赋能
在浙江某精密模具企业,4台数控机床通过桁架机械手串联组成柔性产线,实现“黑灯工厂”改造:
- 效率提升:单班次产能从120件提升至400件,换型时间由45分钟缩短至8分钟;
- 成本优化:人力投入减少70%,每年节省人工成本超80万元;
- 良率改善:加工尺寸一致性达到99.3%,刀具损耗率下降60%。
此外,在军工、医疗器械等领域,桁架机械手的洁净室适配版本已成功应用于高精度光学元件加工,通过真空吸盘或定制化夹具,实现脆性材料的无损搬运。
四、未来趋势:轻量化与模块化并行发展
为适应中小型企业的降本需求,新一代桁架机械手正朝着轻量化、即插即用方向演进:
云端远程运维功能可实时监测设备状态,提前预警潜在故障,进一步减少停机损失。
碳纤维复合材料的应用使设备自重降低40%,同时保持高强度特性;
标准化接口设计支持机械手与不同品牌数控机床的快速对接,部署周期缩短至3天;
该内容为原创,转载请注明:http://www.zdh360.com/ 嘉辉上下料机床桁架机械手