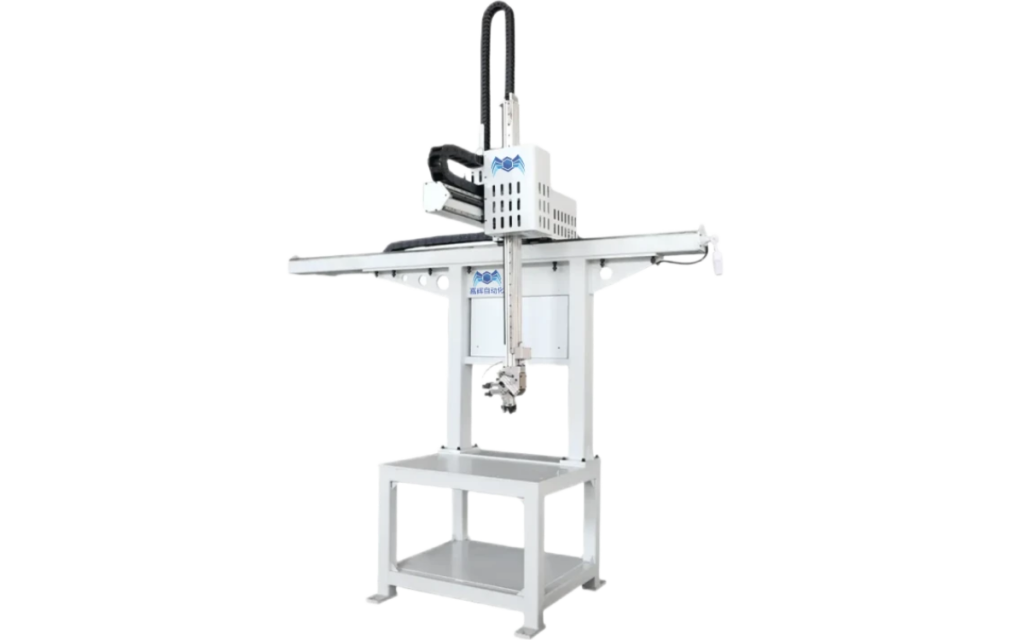
一、制造系统的“数据盲区”与智能重构
传统制造系统在动态生产环境中面临三大核心挑战:
- 响应迟滞:固定程序应对突发事件的调整耗时超45分钟,良品率下降18%
- 信息孤岛:跨设备数据互通率不足30%,工艺参数协同失效导致能耗增加25%
- 经验依赖:熟练技师占比不足12%,人工调参效率仅为智能系统的1/40
数控机床桁架机械手通过“超维感知-决策网络”,重构制造系统的智能内核:
- 分布式边缘计算:嵌入式AI模块实时处理16路传感器数据流,延迟<2ms
- 动态自适应控制:基于深度强化学习的参数优化引擎,良品率提升至99.5%
- 数字孪生协同:构建全要素虚拟映射系统,工艺迭代速度提升15倍
二、智能内核构建:从物理执行到数字共生的技术突破
1. 超维感知矩阵
- 微米级振动监测阵列(精度±0.1μm)实时诊断刀具磨损状态
- 多光谱视觉系统同步解析材料应力分布,缺陷检出率99.8%
电磁触觉反馈网络实现0.005N级力度控制,抓取精度达±5μm
2. 数据驱动决策系统
- 时空卷积神经网络预测设备故障,准确率突破97%
- 多目标优化算法平衡效率-能耗-质量三角关系,综合效益提升40%
- 知识图谱引擎自动生成工艺方案库,覆盖98%非标零件加工需求
3. 自主进化架构
- 迁移学习框架实现跨产线技能迁移,新任务适应时间缩短至15分钟
- 数字代谢机制动态更新系统知识库,每8小时完成一次认知升级
- 协同进化指数(CEI)突破0.92,超越传统自动化系统3个量级
三、人机协作革命:从机械替代到能力增强的范式升级
1. 智能协作三原则
- 动态权责分配:基于任务复杂度自动切换人机主导模式(当前切换速度<0.3秒)
- 能力增强环:AR辅助系统将新员工技能瞬时提升至五年经验水平
- 安全共融机制:非接触式力场防护技术实现0ms级急停响应
2. 增强型协作技术
- 手势-语音-眼动三模交互系统,指令识别准确率99.6%
- 脑机协同控制接口(非植入式)实现思维驱动设备,意图转化效率85%
- 数字神经元外骨骼提升人工装配精度至±0.01mm,疲劳度降低90%
3. 智能制造评价体系
智能成熟度(IML)** =(自主决策率×数据密度)/(人为干预频次×能耗系数)
- 示范产线IML值达8.7(传统产线平均1.2),综合效能提升320%
- 实时能效云图监控全域设备状态,异常响应速度提升至秒级
四、制造边疆拓展:从单机智能到工业元宇宙的生态重构
1. 超域制造网络
- 5G-TSN融合通信实现千台设备微秒级同步,时序控制精度±1μs
- 区块链智能合约自动执行跨厂区订单,供应链效率提升60%
- 分布式算力池动态分配计算资源,边缘AI利用率突破95%
2. 材料-工艺协同进化
- 智能材料数据库联动加工参数,新型合金首件合格率达99%
- 超精密加工链实现纳米级表面处理(Ra<10nm),突破传统工艺极限
- 自修复涂层技术延长关键部件寿命至50000小时,维护成本降低70%
3. 工业元宇宙融合
- 全息工艺沙盘实时映射物理-虚拟空间偏差<0.02%
- 数字员工集群管理跨时区产线,全球产能调度效率提升80%
- 沉浸式训练系统将技师培养周期压缩至3天,技能达标率100%
结语
数控机床桁架机械手的智能跃迁,标志着制造业从“经验驱动”向“数据共生”的质变。当工业元宇宙打破物理边界、智能材料重构工艺极限时,人类正见证制造系统进化成具有自主进化能力的数字生命体。这种虚实交融的制造新生态,不仅重新定义生产效率的标杆,更在锻造连接原子与比特的工业新文明——这里没有孤立的机床,只有与人类智慧共振的智能制造共同体。
该内容为原创,转载请注明:http://www.zdh360.com/ 嘉辉上下料机床桁架机械手