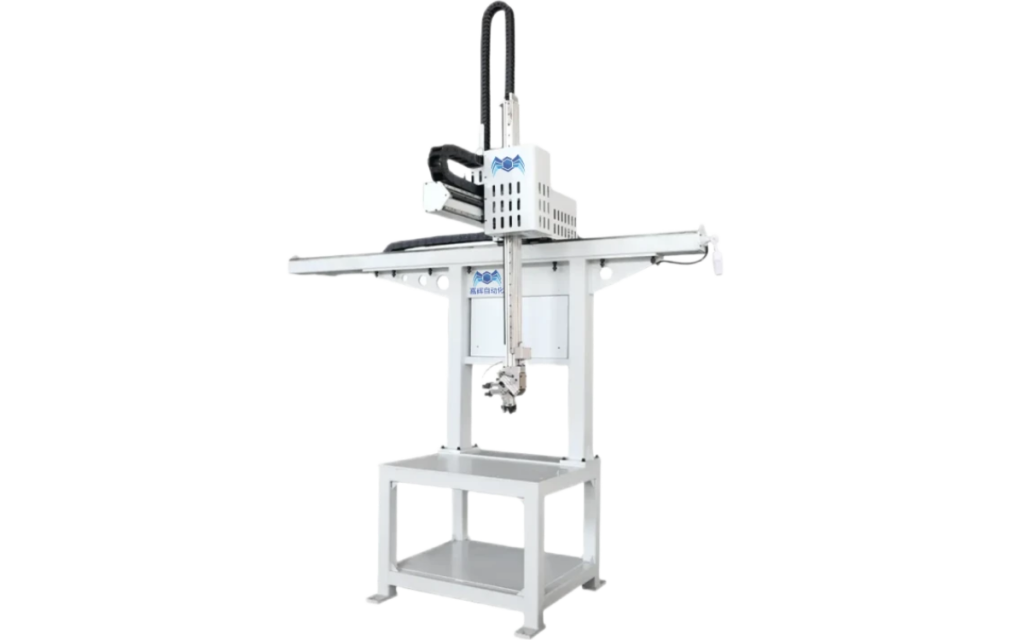
一、传统制造的效率困局与升级拐点
在制造业转型升级的浪潮中,数控机床的高效潜能常被传统上下料模式束缚,形成三大核心矛盾:
时间损耗陷阱:人工换料导致的设备空转率普遍超过30%,日均产能损失达4.2小时
精度波动黑洞:人工装夹0.05-0.2mm的随机误差,使批量加工废品率较自动化产线高3-5倍
成本失控循环:三班倒人力配置使单台机床年均人工成本突破20万元,且面临技工短缺风险
行业数据显示,2023年中国数控机床自动化渗透率仅为41%,但采用桁架机械手的企业设备综合效率(OEE)平均提升至89%,印证自动化已成为破解制造瓶颈的必选项。
二、技术内核:桁架机械手的精密控制体系
作为工业自动化的“精度引擎”,现代桁架机械手通过四大技术支柱构建核心竞争力:
- 刚柔耦合的机械架构
拓扑优化设计的桁架结构,动态刚性提升至35000N/mm²,自重减轻40%
直线电机驱动系统实现±0.003mm定位精度,重复定位稳定性达99.99%
模块化快换接口兼容12种末端执行器,5分钟内完成产线换型
- 闭环控制系统
光栅尺+磁栅双反馈机制,实时补偿温度漂移与机械间隙
自适应振动抑制算法将运动冲击降至0.2G以下,保护高价值工件
故障预诊断系统通过200+传感器参数,实现150小时故障预警
- 能效优化网络
再生制动技术回收92%制动能量,综合能耗降低38%
智能休眠模式使待机功耗低于5W,年省电超10万度
微量润滑系统减少80%的维护耗材消耗
- 智能交互平台
数字孪生系统实现虚拟调试,缩短70%产线部署周期
开放式API接口支持与MES/ERP系统无缝对接,数据采集颗粒度达毫秒级
5G边缘计算模块实现多设备协同决策,响应延迟压缩至10ms以内
三、产业价值:重构制造逻辑的三大维度
桁架机械手的应用正在改写制造业底层逻辑:
效率重构
设备利用率从行业平均65%提升至93%,单机年产值增加超150万元
换料节拍缩短至5秒级,较人工操作效率提升400%
连续生产周期突破30天,实现真正“黑灯工厂”
质量跃迁
装夹重复定位精度稳定在±0.005mm,CPK值从1.0优化至2.5
工艺一致性使产品寿命标准差缩小78%,质量损失成本下降90%
管理革新
生产数据全流程数字化,工艺优化周期从周级压缩至小时级
人力需求减少80%,技术工人转向高价值维护与编程岗位
设备状态透明化,备件库存周转率提升3倍
四、技术前沿:下一代桁架机械手的进化方向
在工业4.0与智能制造双轮驱动下,桁架机械手正经历三大革命性升级:
- 超精密化
量子传感技术突破经典物理限制,定位精度向±0.0001mm迈进
超低温冷却系统消除材料热变形,温漂误差趋近于零
- 智能化跃迁
类脑芯片实现自主路径规划,动态避障决策耗时<1ms
联邦学习框架构建跨产线知识库,工艺自优化准确率达99.9%
- 可持续化设计
4D打印自修复材料使设备寿命突破20万小时
碳足迹追踪模块自动生成绿色制造报告,能耗强度降低45%
结语
数控机床桁架机械手已从单一自动化设备进化为智能制造系统的核心节点。其通过精密控制、数据融合与智能决策构建的“技术三角”,不仅破解了传统制造的效率与质量困局,更在重构全球制造业的价值分配规则。当工业竞争进入“微米级精度、毫秒级响应”的新纪元,对桁架机械手的技术深耕,将成为企业突破产业升级“达尔文海”的关键方舟。
该内容为原创,转载请注明:http://www.zdh360.com/ 嘉辉上下料机床桁架机械手