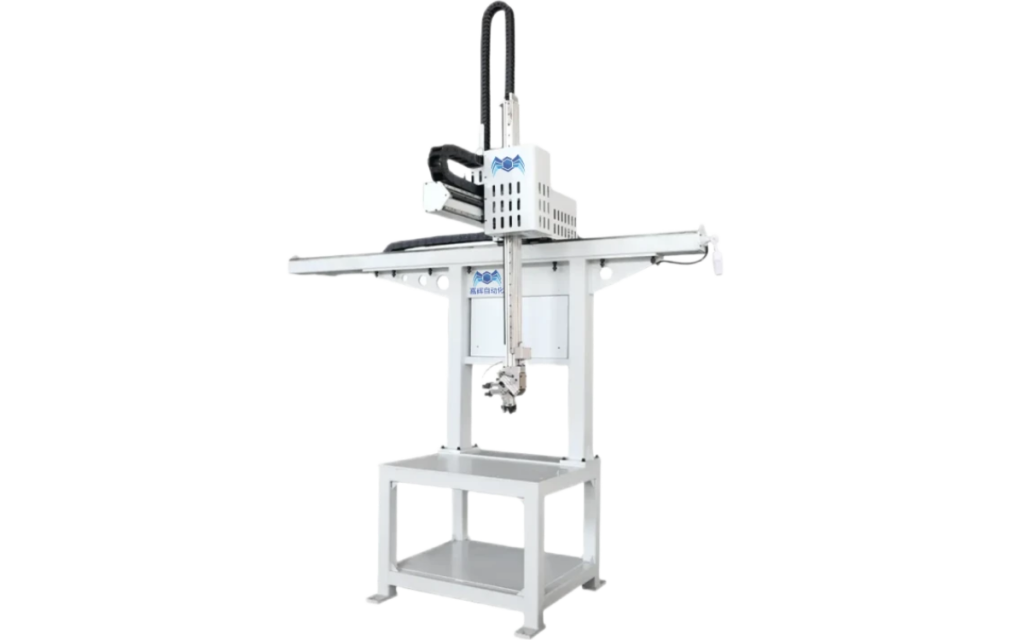
在 智能制造2.0 时代,工厂正从“自动化”向“自主化”跃迁。数控机床桁架机械手 作为生产线核心执行单元,通过与 工业物联网(IIoT) 和 数字孪生技术 的深度融合,正在实现 设备全生命周期管理 和 零停机生产 的革命性突破。
一、工业互联时代的三重挑战
- 设备状态透明化不足
- 传统机械手依赖人工巡检,故障发现滞后导致 非计划停机损失占比达30%;
- 解决方案:部署 振动传感器+温度传感器+电流监测模块 ,实时采集 100+项运行参数,异常识别准确率达98%。
- 生产数据孤岛效应
- 机械手与数控机床、MES系统间缺乏数据互通,工艺优化效率低下;
- 案例:某汽车零部件企业通过 OPC UA协议 实现多设备数据贯通后,换型时间缩短40%。
- 能耗与效率矛盾
- 未优化的运动轨迹导致 空行程能耗占比超25%;
- 技术突破:基于 数字孪生仿真 的路径优化算法,使能耗降低18%,节拍时间提升12%。
二、智能桁架机械手的四大核心技术
- 边缘计算赋能实时决策
- 本地部署轻量化AI模型,支持 微秒级响应 的轨迹纠偏与负载自适应;
- 数据对比:传统PLC控制延迟约50ms,边缘计算架构下延迟降至2ms内。
- 5G+工业互联网深度融合
- 通过 5G专网 实现 1000Mbps带宽 的低时延通信,支持远程编程与跨厂区协同作业;
- 场景验证:某新能源电池企业利用5G远程操控桁架机械手完成 2000公里外产线调试。
- 数字孪生驱动预防性维护
- 构建 1:1虚拟映射模型 ,模拟机械手寿命曲线与故障概率分布,预测准确率高达95%;
- 效益:备件更换周期从平均3个月延长至18个月,维护成本下降60%。
- 自适应控制算法
- 开发 强化学习算法 ,根据加工材料硬度、刀具磨损状态动态调整 压力补偿参数;
- 实测结果:不锈钢加工表面粗糙度Ra从3.2μm稳定控制在1.6μm以内。
三、六大行业落地场景与ROI测算
行业 | 应用场景 | 技术配置 | 投资回报周期 |
---|---|---|---|
新能源汽车 | 动力电池模组装配 | 视觉定位+力反馈系统 | 8-10个月 |
航空航天 | 复合材料叶片精加工 | 真空吸附+多轴振动抑制 | 12-15个月 |
食品包装 | 灌装线柔性切换 | RFID物料识别+轻量化机械臂 | 6-8个月 |
电子装配 | SMT贴片高速定位 | 高频振动过滤+纳米级伺服 | 9-11个月 |
光伏硅片 | 切片机上下料 | 激光避障+热成像温度监控 | 7-9个月 |
金属铸造 | 浇注机器人路径优化 | 数字孪生仿真+路径重规划 | 10-12个月 |
(ROI测算基于200万级产线改造项目,含硬件投资与3年运维成本)
四、企业智能化升级路线图
- 阶段一:设备联网与数据采集
- 部署低成本 IIoT网关 ,实现机械手运行数据的标准化存储与可视化看板。
- 阶段二:局部场景优化
- 引入 轻量化数字孪生平台 ,针对换型时间、刀具寿命等关键指标进行建模分析。
- 阶段三:全局智能决策
- 集成 工业AI平台 ,打通MES/ERP系统,实现从订单下发到成品交付的全流程自驱。
五、未来演进:从“工具”到“生产大脑”
- 群体协作与自主决策
- 多台桁架机械手通过 UWB定位 组建柔性生产单元,自主规划最优作业路径。
- 能源自洽生态系统
- 集成 光伏储能模块 与 动能回收系统 ,实现机械手自身能源循环供给。
- 人机共融交互界面
- 开发 AR远程指导系统 ,操作员通过智能眼镜实时查看机械手三维状态与维修指引。
结语:重构制造业的价值链
当桁架机械手不再是冰冷的“执行者”,而是具备 感知、思考、决策 能力的“智慧终端”,它将彻底颠覆 离散制造 的底层逻辑。从预测性维护到数字孪生优化,从单点效率提升到全价值链重构,这场由 工业互联 驱动的变革,正在为制造业打开 10倍效率提升 的新空间。
该内容为原创,转载请注明:http://www.zdh360.com/ 嘉辉上下料机床桁架机械手