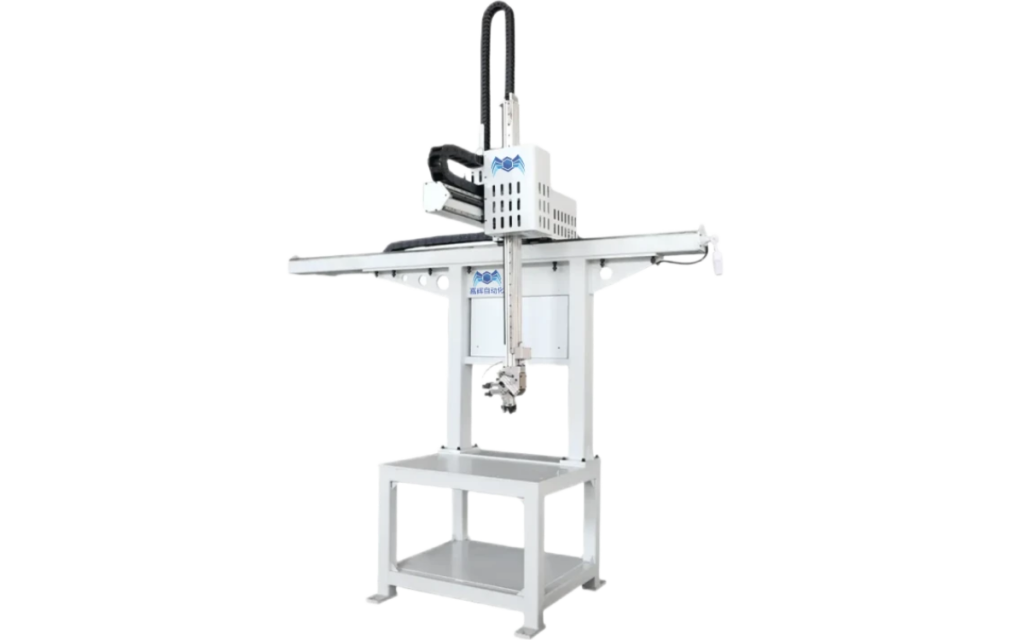
【开篇场景】
凌晨两点的工厂里,某新能源汽车零部件生产线上,最后一批工人正疲惫地搬运着10公斤重的电池托盘。车间主任李工盯着报表上的良品率数据(89.3%),眉头紧锁——这是本月第三次因人工误差导致交付延期。直到遇见嘉辉智能桁架系统,这家企业的命运齿轮开始加速转动…
一、破局时刻:当传统产线遇上智造革命
“上个月我们刚丢掉一个800万的订单,因为人工上下料节拍不稳定,导致整线OEE(设备综合效率)卡在68%上不去。”李工在技术交流会上坦言。这是中国制造企业集体焦虑的缩影:
- 用工荒:90后工人离职率高达40%,夜班产能下降35%
- 精度困局:人工重复定位误差±1.5mm,精密件报废率超5%
- 转型阵痛:传统设备改造成本高,停机风险难承受
嘉辉工程师王磊展示了一组数据:搭载视觉的桁架机械手,可在72小时内完成部署,良品率稳定在99.6%以上。这直接击中了客户的痛点。
二、柔性进化:一套桁架机械手系统激活整条产线
在签约后的第5天,嘉辉技术团队带来了模块化智能桁架系统:
- 智能换型:磁吸轨道+参数化编程,产线切换从4小时压缩至18分钟
- 视觉赋能:3D视觉定位误差±0.03mm,比老师傅“手感”更可靠
- 人机共生:操作工转型为系统管理员,人力成本直降60%
真实改造场景:
“最让我震惊的是桁架机械手处理异形件的能力。”李工回忆道,“过去需要定制工装的不规则散热片,现在AI视觉自动生成抓取路径,调试时间从3天变成扫码即用。”
三、数字孪生:在虚拟世界预见未来
在部署阶段,嘉辉工程师打开数字孪生平台,虚拟产线开始同步运行:
- 风险预判:提前发现2处机械干涉点,规避50万元潜在损失
- 效能优化:通过模拟计算找到最优加速度曲线,节拍从15秒提至9.8秒
- 人才孵化:AR操作指导系统让新员工3天独立上岗
“就像给生产线装了‘预知眼’,我们甚至能预测3个月后的设备维护节点。”生产总监张总在验收会上感叹。
四、看得见的回报:从成本中心到利润引擎
投产90天后的关键数据:
指标 | 改造前 | 改造后 | 提升幅度 |
---|---|---|---|
单日产能 | 3200件 | 5800件 | 81% |
单位能耗 | 1.8度/件 | 0.9度/件 | 50% |
质量索赔率 | 2.3% | 0.15% | 93% |
紧急停机次数 | 12次/月 | 0次/月 | 100% |
更惊喜的是,这套系统成为企业获取订单的技术背书——某国际车企在看到数字化车间实景后,直接将订单量追加300%。
【客户证言】
“过去总觉得智能制造是巨头的游戏,嘉辉的‘轻量化改造’方案让我们明白:转型不需要推倒重来,而是给传统产线注入智能基因。”
——某新能源科技公司生产副总裁 陈总
五、未来已来:你的工厂离「灯塔」还有多远?
当行业还在讨论“机器换人”时,嘉辉已定义智能生产新标准:
- 极速响应:7天完成从需求对接到试产验证
- 无限拓展:开放API接口,无缝接入MES/ERP
- 低碳承诺:每台设备全生命周期减碳12.8吨
现在行动的企业正在收割三大红利:
- 政策红利:申报智能工厂最高获800万补贴
- 成本红利:人力+能耗双降带来的边际效益递增
- 市场红利:获得头部客户「数字化供应商」认证资格
让明天的工厂,从今夜开始进化。