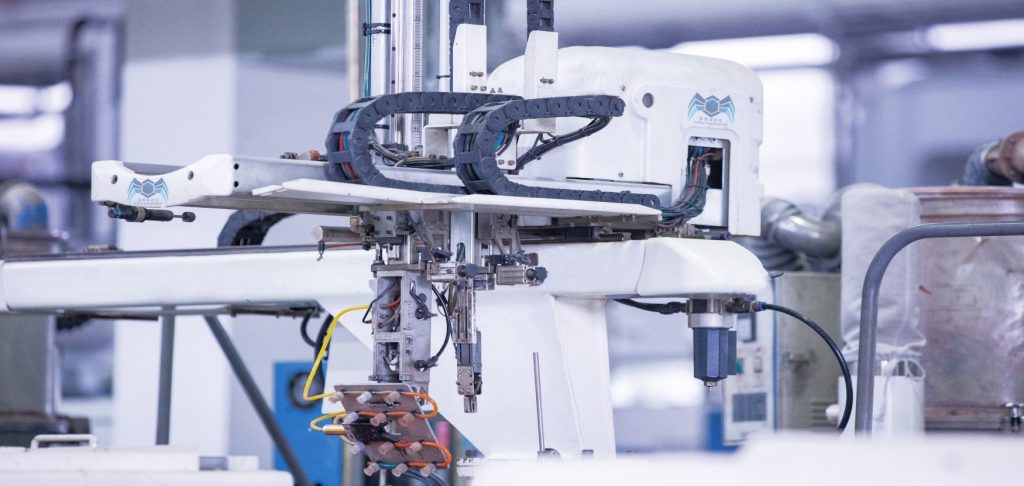
一、案例背景
某大型汽车制造企业,随着汽车市场需求的不断增长,对发动机的产量和质量提出了更高的要求。在发动机生产过程中,传统的人工上下料方式存在效率低下、劳动强度大、精度难以保证以及工伤风险高等问题,严重制约了生产效率的提升和产品质量的稳定性。为了改变这一现状,企业决定引入上下料桁架机械手系统,以实现发动机生产的自动化升级。
二、应用场景与需求分析
在发动机缸体、缸盖等零部件的加工环节,需要将毛坯件准确地放置到数控机床的加工台上进行铣削、钻孔、镗孔等一系列加工操作,加工完成后再将成品件取下并搬运至后续检测或装配工位。由于发动机零部件体积较大、重量较重且形状复杂,对上下料的精度、速度和稳定性要求极高。同时,生产线上有多台不同型号的加工设备,需要机械手能够灵活适应不同的工作任务和工作环境,实现与整个生产线的无缝对接和协同作业。
三、解决方案实施
- 机械手选型与定制
- 根据发动机零部件的尺寸、重量和生产节拍,选择了一款负载能力为 500kg、工作半径达 5m 的大型上下料桁架机械手。其机械结构采用高强度钢材焊接而成,确保足够的刚性和稳定性,X、Y、Z 轴均配备高精度滚珠丝杠和直线导轨,以及高性能伺服电机,保证了定位精度可达 ±0.1mm,满足了发动机加工的精度要求。
- 针对发动机缸体和缸盖独特的形状和抓取点,专门设计了定制化的夹具。夹具采用液压驱动,能够提供足够的夹紧力,同时配备有压力传感器和位置传感器,确保在抓取和放置工件时的可靠性和安全性。
- 控制系统集成
- 采用先进的 PLC 控制系统作为核心控制单元,通过工业以太网与车间的 MES(制造执行系统)和 DNC(分布式数控系统)进行连接,实现了生产数据的实时交互和远程监控。
- 在机械手上安装了视觉识别系统,由高分辨率摄像头和智能图像处理软件组成。视觉系统能够快速准确地识别工件在料架上的位置和姿态,将坐标信息传输给控制系统,从而引导机械手进行精准的抓取动作,有效提高了上下料的自动化程度和准确性,即使在工件摆放位置存在一定偏差的情况下,也能顺利完成抓取任务。
- 生产线布局优化
- 对发动机生产车间的生产线进行了重新布局,将上下料桁架机械手合理地安装在数控机床之间,优化了物料传输路径,减少了物料搬运的时间和距离。同时,在机械手周围设置了安全防护围栏和光幕传感器,确保操作人员的人身安全,当有人员进入危险区域时,机械手能够立即停止运行。
四、应用效果
- 生产效率显著提升
- 上下料桁架机械手投入使用后,发动机零部件的上下料时间由原来的平均 5 分钟 / 件缩短至 1 分钟 / 件,生产效率提高了 400%。这使得单条生产线的日产量从原来的 30 台发动机增加到 120 台,大大满足了市场对发动机的需求增长,为企业带来了显著的经济效益。
- 产品质量稳定性提高
- 由于机械手的高精度定位和稳定的抓取放置动作,有效避免了人工操作中可能出现的碰撞、划伤等质量问题,发动机零部件的加工精度得到了更好的保证,产品的废品率从原来的 3% 降低至 0.5% 以下,提高了产品的质量和可靠性,增强了企业的市场竞争力。
- 降低劳动强度和人力成本
- 原来每条生产线需要 8 名工人负责上下料工作,采用机械手后,只需 2 名工人进行监控和设备维护,大大减轻了工人的劳动强度,同时减少了人力成本支出。每年节省的人力成本达到数百万元,使企业在人力资源配置上更加合理和高效。
- 生产数据管理与追溯性增强
- 通过与 MES 系统的集成,上下料桁架机械手能够实时上传生产数据,如上下料时间、工件批次、加工设备状态等信息,实现了生产过程的数字化管理。这些数据为企业的生产计划制定、质量分析和设备维护提供了有力依据,同时也方便了产品的质量追溯,一旦出现质量问题,能够迅速定位问题源头,采取有效的改进措施。
五、经验总结与展望
通过在汽车发动机生产中应用上下料桁架机械手,企业成功实现了生产自动化升级,取得了显著的经济效益和社会效益。在实施过程中,企业深刻体会到了选型定制、系统集成和生产线布局优化的重要性,这些因素直接影响到机械手的应用效果和投资回报率。
展望未来,随着智能制造技术的不断发展,上下料桁架机械手将朝着更加智能化、柔性化和高效化的方向发展。例如,通过引入人工智能算法,使其能够自主学习和适应不同的生产任务和工况变化,进一步提高生产效率和产品质量;同时,加强与其他智能设备的互联互通,构建更加完善的智能制造生态系统,为汽车制造等行业的发展提供更加强有力的支持。